What inspection should be done for daily maintenance of pneumatic pulverizer?
After the use of air grinder, the work efficiency of all walks of life has also been improved. The equipment uses air separation, heavy pressure grinding and shearing to achieve ultra-fine grinding of dry materials. According to the bonding characteristics of petroleum coke powder, the structural design of grinder and classifier is optimized, which solves the problem of binder and improves the production without large particles.
It is necessary to check whether the power socket, power cord and plug of the pneumatic pulverizer have the problem of oxygen shedding and fracture. If not, plug in the power supply and try the machine. When the motor is powered on and does not rotate, and the wheel can rotate again with a light hand, it can be concluded that it is caused by the failure of one of the two starting capacitors of the machine. If the spark and sound are weak, it means that the capacity of the capacitor has decreased, and it needs to be replaced or added with a small capacitor; If the discharge spark can be emitted and there is a loud crackle at this time, the capacitor can be used. If the capacitor material has been damaged and short circuited, we can't use this method, and we need to replace it with a new one of the same specification.
Check the lubrication of the bearing and check that all fasteners are tight.
Check whether the transmission belt of the system is installed correctly and in good condition. If the belt is damaged, it should be replaced in time. When there is oil stain on the belt or pulley, it should be wiped with a clean cloth in time.
Check whether the protective device is in good condition. If it is found unsafe, it should be eliminated in time.
Check whether there are materials or other sundries in the damaged cavity, if any, it needs to be cleaned in time.
Check whether the hydraulic jacking machine plug or jack screw is returned, and whether the adjusting gasket is installed correctly and pressed tightly.
During the operation and development, check the compressed air pipeline for air leakage at least once per shift, and discharge the water accumulated in the oil-water separation triplet once.
Check the discharge door once a week to see if there is water leakage, whether the sealing strip is broken, and whether the discharge linkage is in the dead point when closing.
I hope the above sharing can help you and your operation in the future.
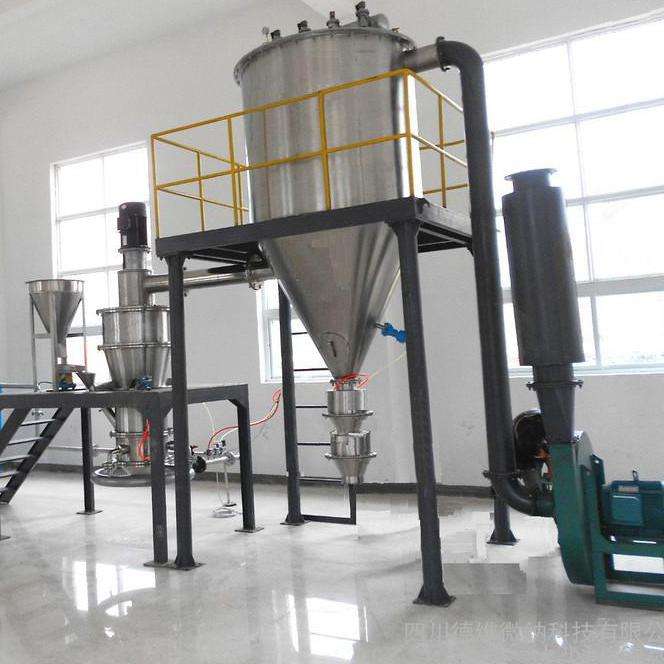