SCR denitration technology
SCR denitration technology
1. Principles and characteristics of SCR denitration technology
SCR denitration technology, namely Selective Catalytic Reduction (Selective Catalytic Reduction) means that under the action of catalysts (such as TiO2, V2O5, WO3), the reducing agent NH3 reduces NO and NO2 in the flue gas to non-toxic at 290-400℃ The N2 and H2O, and almost no NH3 oxidation reaction, thereby reducing NH3 consumption.
2. SCR denitration system and process
The SCR denitration system sprays ammonia or other suitable reducing agents into the flue gas upstream of the catalyst, and uses the catalyst to convert the NOx in the flue gas into N2 and H2O. In the operation of the system, the ammonia is first evaporated, and then mixed with the dilution air or flue gas, and sprayed into the flue gas upstream of the SCR reactor using the ammonia injection grill. SCR denitration system mainly includes: reactor system; flue gas system; reducing agent storage, preparation and filling system; soot blowing system.
2.1 Reactor system
The reactor system is the catalyst system. The catalysts in the SCR denitration system have three types: honeycomb type, plate type and corrugated type.
The chemical life of the catalyst is guaranteed by the monomer catalyst activity and the overall volume. The performance of the catalyst during the chemical life can meet the requirements, and the catalyst balance plays a key role.
The chemical composition of SCR catalyst is as follows:
Carrier composition: TiO2 (>80%);
Main active ingredients: V2O5 (<2%); WO3: Improve the activity of the high temperature section, while inhibiting the oxidation rate, enhancing thermal stability, and preventing the reduction of specific surface area caused by sintering; MoO3: Improve the As poisoning ability.
Other ingredients: SO, inorganic oxides other than titanium, etc.;
Structural components: glass fiber, etc. (reinforcement), polyethylene oxide, etc. (binder).
2.2 Flue gas system
Through digital and physical model tests, a multi-layer uniform distribution device is set before the entrance of the reactor to realize the uniform distribution of dust, flue gas, temperature and nitrogen oxides on the cross section of the reactor.
2.3 Reductant storage, preparation and filling system
SCR denitrification systems generally use liquid nitrogen, ammonia, and urea as reducing agents. The SCR system consists of an ammonia supply system, an ammonia/air injection system, a catalytic reaction system, and a control system. In order to avoid the energy consumption of flue gas reheating, the SCR reactor is generally placed after the economizer and before the air preheater. That is, the high dust section layout. Ammonia is added in the horizontal pipe before the air preheater and mixed with the flue gas. The catalytic reaction system is the core of the SCR process. It is equipped with NH3 nozzles and fly ash purging devices. The flue gas enters the SCR reactor loaded with the catalyst along the flue, and catalytic reduction of NH3 to N2 occurs on the surface of the catalyst. The catalyst is the key to the entire SCR system. The design and selection of the catalyst are determined by the flue gas conditions and components. The three interaction factors that affect its design are the NOx removal rate, the NH3 escape rate and the catalyst volume.
3. Technical support and advantages
CFD simulation test items mainly include: SCR reactor flow field distribution test, SCR reactor NH3/NOx mixing test, SCR system pressure loss test, SCR reactor ash accumulation test.
The main advantages of SCR denitration technology are as follows:
⑴ Adapt to different flue gas conditions;
⑵Ensure the effective mixing of ammonia and flue gas;
⑶ Reduce the number of ammonia injection points by more than 90% (usually 3-8 ammonia injection points);
⑷ Minimize the risk of nozzle blockage caused by ammonium salt;
⑸Simplify the debugging procedure and shorten the debugging time;
⑹ Regardless of the load changes and the complicated operating conditions, the company always meets the promised value of denitrification efficiency and ammonia escape rate.
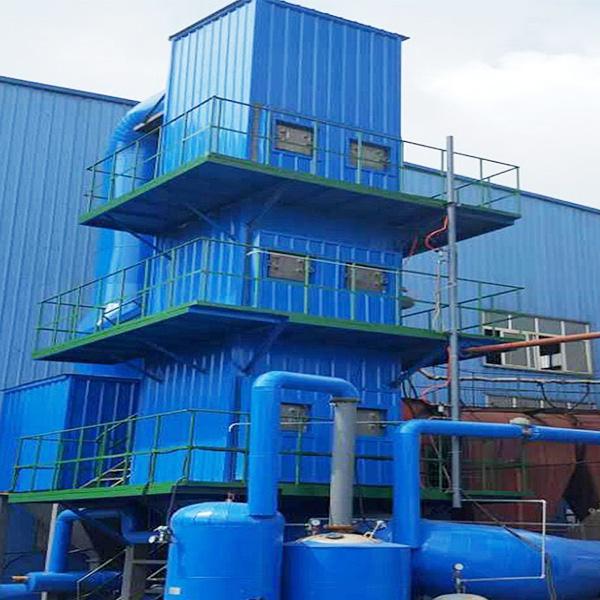